Family of Cobalt Alloys
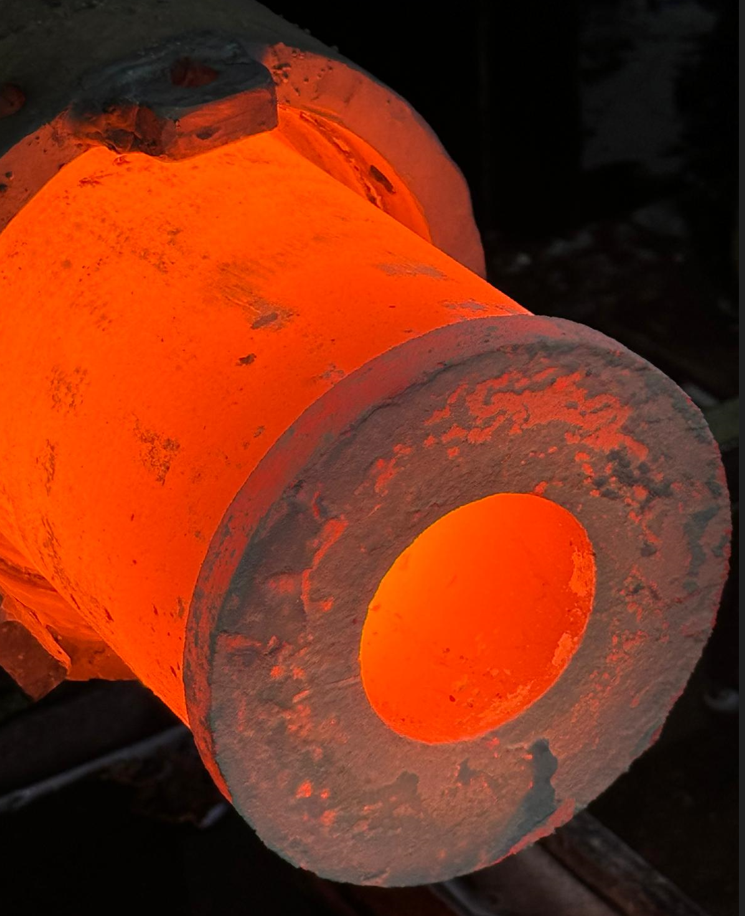
The Haynes Corp invented the family of cobalt-based alloys more than 100 years ago. Cobalt-based alloys are extensively employed in many industries to address wear resulting from corrosion and thermal conditions.
The purpose of cobalt alloys is the reduce the effect of friction and not lose strength until above 600C. They have corrosive resistance down to 3 PH thanks to the amount of Nickel. The trademark name of “Stellite” belongs to Kennametal as a registered name. Focus Casting and Engineering Co. produces generic alloys with their own names. These alloys tend to be costly, with their pricing primarily determined by the market value of cobalt. The Price policy directly depends on the market price of Cobalt, also the overall expense is affected by the increased complexity associated with the rapid machining of these alloys.
There are no particular heat treatment protocols mandated, aside from those aimed at stress relief. This is due to the fact that the properties of these alloys remain stable and unaffected by heat treatment. Once the alloy has solidified, its characteristics cannot be modified. The propensity of cobalt alloys to fracture or develop cracks limits the application of solid components in numerous instances.
These alloys, including Cobalt Alloy4, Cobalt Alloy6, Cobalt Alloy12 and Cobalt Alloy800 acquire their wear resistance during the transition from liquid to solid in the casting process. The hardness of these alloys is influenced by the quantity and dimensions of the carbides that form during this phase change. The alloying elements, which include iron, silicon, tungsten, and chromium, react with carbon to create carbides. A significant challenge arises from the rapid formation of these carbides, with the duration of this process being contingent upon the thickness of the cross-section of the component. Generally, a thicker cross-section results in a softer material compared to a thinner one. During the transition, while the overall number of carbides diminishes, the size of the individual carbides increases. This leads to an expansion of the inter-granular spaces between the carbides, resulting in a decrease in hardness. In some cases, the carbides may grow to such an extent that they become dislodged from the matrix during the finishing process.
Focus Casting & Engineering Co. specializes in the molding and pouring of cobalt alloys, ensuring that the casting process cools as rapidly as possible. In this context, cobalt serves as the matrix that binds the carbides together, imparting several beneficial properties to the alloys. Notably, the coefficient of friction is exceptionally low, preventing galling.
Bushes and Sleeves manufactured by Focus Casting & Engineering Co. from cobalt alloys provides long lifecysle and stability of work at Continous Galvinizing lines
Focus Casting & Engineering Co. is consistently prepared to meet specific requirements. Recognizing that their clients are paramount and essential to business success, the company values the patronage of its customers deeply. Furthermore, clients are regarded as integral collaborators in the development of the projects for which they engage Focus Casting & Engineering Co. In the manufacturing sector, the ability to produce highly precise materials and products is of utmost importance to every client.